复合膜产生异味应该如何处理
由于软包装行业长期采用凹印工艺和干式复合工艺,软包装的溶剂残留问题一直未能得到妥善解决。对复合膜的异味残留质量事故,要有一个综合分析,正确判断。一个包装袋从薄膜到成品袋成型,涉及到薄膜、油墨、胶水、溶剂、环境及印刷、复合、熟化等诸多材料和生产工序,如为使薄膜的性能符合制作包装袋的要求,添加了许多的增塑剂、爽滑剂、抗氧化剂、开口剂等,这些助剂在印刷、复合、熟化工艺中的高温作业时,发生了化学反应产生异味,并残留其中,严重影响到食品卫生要求。
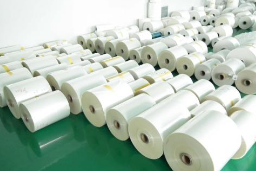
随着GB/T10004-2008标准的出台,软包装企业控制溶剂残留的问题已迫在眉睫。软包装企业必须严格控制溶剂的总量,那么就应该加强原辅材料采购质量的验收、控制,在现有工艺和设备的基础条件下做出最大改进努力。另外,在印刷、复合、熟化各工序中,层层严格控制溶剂的残留量。从几方面结合起来,共同努力,就能将溶剂残留问题降到最低点,以符合食品卫生要求。
在还没有完全使用环保油墨和无溶剂复合前提下,本文从原辅材料、生产、工艺以及生产环境产生异味残留的因素及对策进行分析,与同仁们共享。
一、原辅材料带来的异味
1) 油墨带来的异味
印刷过程中,为了使印刷顺利进行,稀释溶剂中配入一部分高沸点溶剂,这些残留溶剂在印刷收卷前未彻底挥发干净,经过复合烘道烘干后仍然残留在复合膜中,制成的袋子会产生一种异味。国标中要求,一般残留溶剂总量必须在5.0mg/m2以内,其中苯类溶剂不得检出。这样,在印刷过程中残留溶剂量应控制在3.0mg/m2以内最好。印刷膜有异味:主要原因是油墨溶剂残留过多。a)油墨中的溶剂分子与连结料树脂分子间的亲和力过大,导致残留问题加重。b)油墨中混合溶剂挥发速度不一样,配比、控制不当。c)油墨干燥不够彻底。d)不同的薄膜材料对溶剂的吸附不同等原因。因此要合理调配控制混合溶剂,尽量减少挥发慢的溶剂产生残留。不同油墨对溶剂的释放性是不同的,溶剂对油墨中树脂的溶解性越好,则树脂对溶剂的释放性就越差。此外,同一油墨体系中各种色墨的溶剂释放性也有所差别,其中红墨、黑墨的溶剂释放性较差,因此,软包装企业在选择油墨之前,最好向油墨生产企业了解其油墨产品对溶剂的释放性,以便作出相应的处理。
2)胶黏剂的影响
在相同基材、相同工艺下,选用不同生产厂家的胶黏剂,最终生产的复合膜的溶剂残留量也可能不一样。这是因为聚氨酯胶黏剂主剂分子键中含有活性羟基(-OH),与乙酸乙酯(CH3CH2OCH3)会形成氢键,从而大大束缚了乙酯的挥发。而胶黏剂主剂成分的变化会影响氢键的强弱,氢键越强,对乙酸乙酯的释放越难,因而不同厂家的胶黏剂会造成不同的溶剂残留结果。
胶粘剂如果反应不完全,也会产生一种单体味,这种游离单体如果在复合膜中存在,放置时间多长都不会跑掉。聚氨酯胶粘剂因,稀释选择醋酸乙脂溶剂加入,其纯度要求总含量在99%以上,因为固化剂中的异氰酸酯非常活泼,一碰到水立即反应生成胺或二氧化碳。据有关资料研究,水与异氰酸酯的反应比与主剂的反应快20倍。因此控制醋酸乙酯溶剂中水加醇的总含量十分必要。在干式复合中,对醋酸乙酯含水和醇的量不能超过0.2%,国外对用在干式复合中的醋酸乙酯规定是水和醇的总含量不能超过0.05%。
不同的双组份聚氨酯粘合剂对水和醇的敏感度都不一样,如PU-1951/PU-1975H型胶粘剂对水和醇的敏感度是0.7~1.0之向,在生产中若胶粘剂对水和醇的敏感度超出这个范围,可能造成复合不干、异味、变硬、变脆现象。
3)溶剂质量、特性带来的影响
如果采用含有甲苯的溶剂型油墨,则印刷后必然会有甲苯的残留,残留的甲苯会进一步影响胶黏剂中的乙酸乙酯的挥发,一般乙酸乙酯的最终残留量是甲苯残留量的1.5~2.0倍左右。
乙酸乙酯中的水分影响了乙酸乙酯的挥发,进而影响复合膜的溶剂残留量。所以应选用纯度较高的乙酸乙酯。稀释剂乙酸乙酯中不能含如水、醇、胺等杂质。否则在配制时易与固化剂异氰酸酯反应,造成粘合剂配制比例失调,并且产生CO2造成气泡。同时也会降低乙酯的挥发性。
4)薄膜对溶剂残留量的影响
不同的涂胶薄膜基材对溶剂的吸附和释放速率是不一样的。常用的涂胶薄膜基材对酯类的释放速率为:PET>NY>BOPP(吸附速率相反)、对芳香烃类的释放速率为:CPP>OPP>PET>BOPA。